Алмазний диск по бетону: різка та шліфування
Для різання пористих, пористих і важких бетонів, каменю і цегли в даний час використовується алмазна різання, для якої застосовуються диски, канати, коронки (фрези) і ланцюги - весь цей інструмент має діамантове напилення. Така різка досить широко застосовується для виготовлення всякого роду отворів при монтажі комунікацій, для облаштування дверних і віконних прорізів, ніш, для часткового або повного демонтажу будівель і конструкцій. Більш детально про такий інструмент мова піде нижче, а також ви зможете подивитися тематичне відео в цій статті, як додаток до матеріалу.
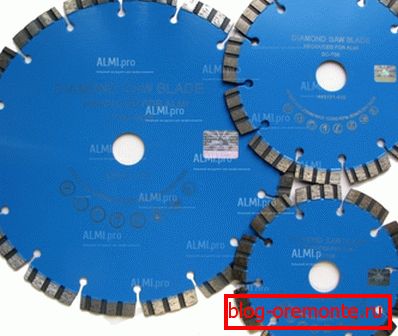
Нюанси алмазного різання
Примітка. Існує небезпечна помилка, що алмазний диск по залізобетону в стані різати не тільки сам бетон, а й арматуру, яка знаходиться всередині нього. Це абсолютно не так - при зіткненні обертового на великій швидкості диска з металом діамантове напилення моментально розплавиться. Хто користувався такими колами, міг помітити, що напилення наноситься збоку, а ось стирається з торця, тобто, при терті зменшується не товщина, а діаметр. Значить, якщо ви захочете перерізати арматуру, то відбудеться безпосередній контакт двох металів, що і призведе до оплавлення диска, як більш тонкого матеріалу. Такий процес неможливий по законам фізики!
технологія різання
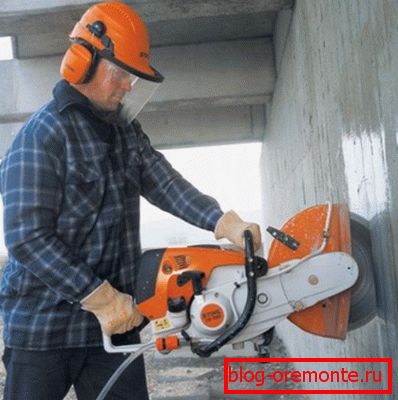
- Вперше така техніка виникла в 60-ті роки минулого століття в Західній Європі, але залізобетонні конструкції поширювалися теж по всьому світу, принісши з собою і способи їх найбільш продуктивною обробки. У загальних рисах алмазна різання є досить безпечною технологією, але бетонний пил, яка завжди супроводжує такі процеси, надзвичайно небезпечна для здоров'я - вона може викликати роздратування шкіри, алергію і навіть силікоз (при тривалому вдиханні).
- У зв'язку з цим розроблені різні заходи з техніки безпеки - пиловідсмоктуючі пристрою, шланги для подачі води, а на крайній випадок - звичайний респіратор із захисними окулярами. Є багато обладнання, яке розроблено з готовими захисними засобами, серед яких німецький STIHL і EIBENSTOCK, американський ISC BLOUNT INO, шведський HUSQVARNA, австрійський TYROLIT HYDROSTRESS і так далі.
- Подібне обладнання представлено дисковими і ланцюговими бензорізи, стінорізними машинами, де диск може досягати до 16000 мм в діаметрі з глибиною занурення до 730 мм (їх ціна досить висока) і, нарешті. Кутові шліфувальні машини (болгарки), де найбільший диск має 400 мм в діаметрі і з глибиною різання до 170 мм.
Види алмазних дисків
Примітка. Залежно від того, що ви збираєтеся робити алмазним диском - різати або шліфувати - ви зможете вибрати відповідну конфігурацію сегментів, або взагалі обійтися без таких. Хоча ви зможете будь-яким з них різати майже будь-який з мінералів, але від цього буде залежати швидкість і якість роботи.

- Диск такого типу, як на верхній фотографії чудово підходить для різання таких мінеральних матеріалів, як цегла, камінь, бетон, граніт і кераміка. Сама конструкція кола така, що завдяки сегментам тертя Не завжди і його нагрівання проходить не так інтенсивно, отже, це збільшує його експлуатаційний ресурс. Проте, процес безперервної різання може тривати не більше 1-1,5 хвилини, після чого повинне піти охолодження, як мінімум, 20-30 секунд - такі вимоги являє інструкція від заводу-виготовлювача.

- Якщо діамантове напилення на колі нанесено суцільною смугою, без нарізок, тобто, сегментів, то це говорить про те, що місце зрізу буде більш чітким і рівним, ніж після сегментного руйнування. Це вказує на те, що така конструкція більше підходить для обробки керамічної плитки, мармуру і навіть скла, до того ж, таке коло можна використовувати для шліфування рваних країв різних мінеральних утворень. З огляду на той момент, що в процесі роботи тертя відбувається безперервно, то метал буде грітися сильніше, що в свою чергу викличе оплавлення напилення, тому в таких ситуаціях розумно використовувати водяне проточное охолодження.

- Тепер подивіться на верхню фотографію, на якій зображений комбінований коло, тобто, там немає сегментних нарізів, але також там відсутня суцільна доріжка алмазного напилення - виходить, що саме ця доріжка розбита на сегменти. Така конструкція дозволяє використовувати інструмент, як для мокрої, так і для сухого різання, тобто, ви можете обробляти цегла, бетон, кераміку і мармур і в будь-якому випадку буде хороший результат. Проте, все одно краще використовувати (особливо для точної різки) саме той диск, який для цього призначений - якість роботи від цього підвищується.

- Такі гнучкі диски-черепашки призначені для полірування бетону, мармуру або граніту без застосування водяного охолодження. Алмазне зерно тут має стільникову структуру, яка змонтована на керамічній решітці, що дозволяє відкидати шлам на сторону і в той же час охолоджувати поверхню круга. Такі кола для полірування можуть мати, як форму диска, так і форму чаші.

- А ось тепер ми підійшли до того, про що багато говорять, але погано уявляють - це одночасна різання або шліфування бетону з металом, тобто, такими колами, які зазвичай називають черепашкою, ви зможете перепиляти армований бетонний стовп. Але тут конструкція значно відрізняється від звичного алмазного диска - тут поєднуються особливості шліфувальної алмазної чашки з еластичним кругом. По виду він дуже нагадує звичайний абразив, тільки більш товстий, але в складі містить полімери з мідним порошком, що значно збільшує його зносостійкість і ефективність.
- Звичайно, різання залізобетону алмазними колами такого типу не передбачається безпосередньо - основний акцент робиться на шліфування бетону, але, тим не менш, це цілком можливо, що з успіхом застосовують на практиці майстра-обробники і будівельники. У таких черепашек есть одна особенность, это тип «Металл», который как раз и указывает на то, что ним можно обрабатывать не только минеральные, но и металлические конструкции. Конечно, процесс резки здесь значительно медленнее, чем у любого другого диска с узкой специализированной направленностью, зато возможны вот такие комбинации.
Примітка. Вибір діаметра диска в основному залежить від параметрів інструменту, тобто, можливостей посадкового місця, куди цей диск вставляється.
Знання, які необхідні пересічному споживачеві

Напилення робиться зі штучного каменю, і ці шматочки запресовуються в металеве сполучна речовина, при цьому алмази можуть бути різної величини і різної якості (від чого, власне, і залежить вартість кола), а також різними можуть виявитися сполучні речовини.
Від зміни якості напилення, тобто, якості самого каменю, його концентрації на певній ділянці і складу сполучного компонента отримують необхідні сегменти, за якими вже визначається виробнича спрямованість (суха, мокра або універсальна різка).
Примітно, що для сухого різання на сталеве підстава сегменти кріпляться за допомогою лазерного зварювання, а ось для мокрого різання вони фіксуються срібною пайкою.
На даний момент розроблено нову технологію HDS (HIGH DENSITY SINTRED) - це порошковий пайка високої точності, за допомогою якої напилення проводиться найбільш якісно, з використанням найякісніших сегментів штучного алмазу. Примітно, що така технологія дозволяє використовувати кола з різними сегментами не тільки для мокрої, а й для сухої обробки.
Цей спосіб пайки не залишає нейтральної зони між основною частиною диска і сегментами, отже, тут ріже частина може бути використана на всі 100%.
Совет. Для того чтобы удостовериться, что вы берёте товар именно такого качества, обратите внимание на его этикетку, там должна быть надпись на английском языке «With HDS technology» (с помощью технологии HDS).
Щоб досягти ріжучого ефекту, за допомогою керамічної заточування сегменти відкриваються (сточуються) на глибину, достатню для оголення перших шматочків алмазних зерен. Після цього коло готовий до експлуатації, але у нього є ріжуче напрямок, тому заводи-виробники зазвичай вказують його стрілочками на етикетці. Якщо вони цього не роблять, то напрямок доводиться визначати дослідним шляхом.

Щоб зробити найбільш оптимальний вибір, вам необхідно чітко уявляти, який діаметр і форма зубів підходять для машини, яку ви будете використовувати, а також властивості оброблюваного матеріалу. Звичайно, використовувати коло більшого діаметра, ніж це передбачає несуча машина небажано, тому при потребі краще взяти інший агрегат.
Наприклад, диском на 125 мм ви не зможете 70 мм або 80 мм, тут вам знадобиться коло діаметром 230 мм, отже, для цього потрібно придбати кутову шліфувальну машину (болгарку) великих розмірів, а не знімати кожух з маленькою для установки великого ріжучого елемента - це небезпечно.
Крім того, різним може бути і внутрішній діаметр, тому, його вибирають відповідно з валом шліфувально-ріжучої машини, але якщо вал все-таки виявиться менше, то для цього існують різні насадки. Ні в якому разі не можна затискати коло, коли його внутрішній отвір більше ніж діаметр вала - це в будь-якому випадку приведе до децентралізації і, як наслідок, до поломки диска, а в гіршому випадку, навіть до травматизму.
Найчастіше зустрічаються такі співвідношення внутрішнього і зовнішнього діаметра:
- Для дисків від 155 мм до 230 мм на кутову шліфувальну машину отвір має 22,2 мм (сегменти сухого різання);
- Зовнішній діаметр від 150 мм до 350 мм для верстатної різання отвір становить або 25,4 мм, або 30,0 мм (мокра різання);
- Зовнішній діаметр від 300 мм до 400 мм для асфальтових і ручних різаків мають отвір 25,4 мм (суха і мокра різання).
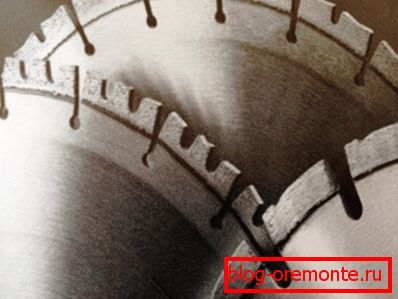
Якщо ви збираєтеся робити будь-який ремонт своїми руками, то вам вже напевно відомий матеріал, з яким доведеться працювати, тому сегментацію вибирайте відповідну - суха або мокра різання. У тому випадку якщо передбачається різнобій, то, звичайно, білите універсальний круг, але їли різати доведеться досить багато, то краще для кожного з матеріалів вибрати відповідну різку.
Не забувайте про те, що різні країни і заводи-виробники можуть використовувати несхожу відмінну маркування, тому, якщо вам незрозуміла напис - звертайте увагу на зуби або їх відсутність і принцип сегментування - про це ми розповідали вище.
При определении типа обрабатываемого материала следует в первую очередь обращать внимание не на его твёрдость или мягкость, а на абразивность - этот фактор более всего «садит» диск. К мягким неабразивным материалам можно отнести мрамор, а к твёрдым - все остекленевшие типа клинкера. А вот гранит или тяжёлый бетон из твёрдых материалов и силикат, шамот или асфальт из мягких можно отнести к абразивной группе.
висновок
На закінчення можна сказати, що для абразивних матеріалів краще вибирати професійні диски, з більш якісним напиленням. Те ж саме можна сказати і про діамантове буріння отворів в бетоні - чим вище якість напилення - тим швидше відбувається процес і більше експлуатаційний ресурс інструменту.